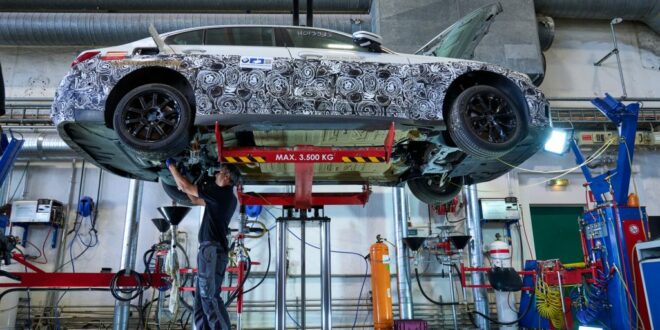
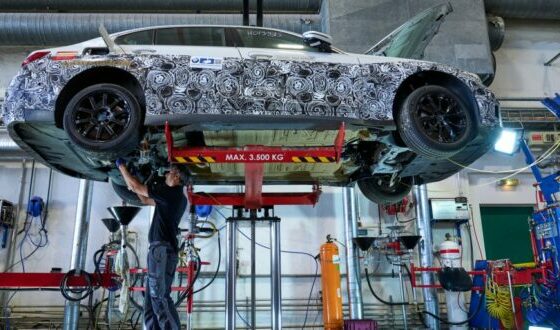
Zöld Közlekedés
A BMW Group már harminc éve mutatja a körforgásos gazdaság irányát
Látványos siker a Car2Car kutatási projektben: az acél, az alumínium, a réz, az üveg és a műanyag hatékony újrahasznosíthatósága.
Az autóipar körforgásosságának továbbfejlesztése érdekében a BMW Group kiemelkedő munkát fektet a modellek teljes életciklusát lezáró újrahasznosítási folyamatok bővítésébe és tökéletesítésébe. A vállalatcsoport Újrahasznosítási és Szétszerelő Központja (RDC – Recycling and Dismantling Centre) már harminc éve fejleszti és teszteli az olyan, újabbnál újabb folyamatokat, amelyek az elhasznált alkatrészek újrahasznosítása és az alkalmazott alapanyagok újrafelhasználása terén jelentős előrelépéseket ígérnek. Az RDC maradéktalanul megosztja tapasztalatait a körforgásos gazdaság szereplőinek globális hálózatával, amellyel nagymértékben járul hozzá az autóipart átfogó körforgásos gazdaság kialakulásához. Az így felhalmozott újrahasznosítási szaktudás a BMW Group terméktervező folyamataiban is visszaköszön, amely garantálja, hogy az új modellek újrahasznosíthatóságával már a tervezési fázisban meghatározó szempontként számolnak a mérnökök.
Az RDC évente több ezer autót hasznosít újra, ezek nagy része előszériás modell, amelyek tesztelési célokat szolgáltak. Szétszerelésüket egy olyan szabványosított folyamat mentén végzik, amelynek középpontjában az újrahasznosítható alkatrészek és az újrafelhasználható alapanyagok felismerése áll.
Az újrahasznosíthatóság tökéletesítésén dolgozó központ a teljes iparág számára mérceként szolgál
Ami 1994-ben egy új, vállalati tulajdonban lévő újrahasznosítási létesítményként indult, az három évtized alatt mára az autók újrahasznosításának iránymutató tudásközpontjává érett. Figyelembe véve az iparág új szabályait és a BMW Group ambiciózus céljait, az RDC a jövőben még fontosabb szerepet tölt majd be: az itt felhalmozott szaktudás kulcsfontosságú a modellek újrahasznosíthatóságának továbbfejlesztésében.
A BMW Group meghatározó szereplőként vett részt a Nemzetközi Szétszerelő-információs Rendszer (IDIS – International Dismantling Information System) kiépítésében, amelyen az RDC megosztja tapasztalatait a körforgásos gazdaság szereplőinek globális hálózatával. Az adatok világszerte díjmentesen érhetők el az újrahasznosítást végző vállalatok számára. A közös tudásbázist jelenleg 41 ország mintegy 3 000 szervezete használja, hogy kitanulja az újrahasznosítható alkatrészek költséghatékony szétszerelését és az értékes alapanyagok hatékony újrafelhasználását.
Az újrahasznosítási folyamatok töretlen fejlesztése és tökéletesítése az ökológiai lábnyom következetes csökkentésére irányuló vállalati törekvés szerves része, miközben az erőforrások megőrzése a károsanyag-kibocsátás redukálását is elősegíti.
A ma hulladéka a holnap nyersanyaga
A modellek újrahasznosítását az RDC az utasbiztonsági rendszerek mérnökien precíz deaktiválásával és szétszerelésével, valamint az összes folyadék leeresztésével és eltávolításával kezdi. A légzsákok pirotechnikáját a BMW Group többek között saját, szabadalmaztatott eljárása mentén semlegesíti. A lengéscsillapítókban dolgozó olajat ugyancsak egy speciálisan erre a célra kifejlesztett eszközzel távolítják el.
Az ezt követő szétszerelési folyamat középpontjában elsőként az egyes alkatrészek újrahasznosítása áll. A sorozatgyártásból származó és újszerű állapotban lévő, működőképes alkatrészeket nem selejtezik le, hanem továbbadják a regisztrált kereskedőknek továbbértékesítésre. Az autó maradék részének mechanikus szétszerelése során egyes anyagokat, így például a kábelkötegekben található rezet egy speciálisan erre a célra kifejlesztett eszközzel választják ki. A motorblokk és a váltó kiemelése után a vázszerkezetet egy külső újrahasznosító létesítményben préselik és aprítják tovább.
A fémek célzott szétszerelése gondoskodik arról, hogy a ma hulladéka a holnap nyersanyagává váljon – a lehető legnagyobb mennyiségben és a lehető legjobb minőségben. Ez nem csupán környezetvédelmi, de pénzügyi szempontból is fontos: a hajtásláncban alkalmazott fémek – a rézhez hasonlóan – rendkívül magas értékkel bírnak. A katalizátor tovább bontása ugyancsak hatékony gazdasági megoldás, hiszen számos értékes nemesfém található benne.
Car2Car: minden részletre kiterjedő kutatási projekt a hatékony újrahasznosítás érdekében
A BMW Group az olyan külső kutatási kezdeményezésekben is aktív szerepet vállal, amelyeknek célja az erőforrások megőrzését és a gazdasági hatékonyság növelését elősegítő, innovatív újrahasznosítási folyamatok kidolgozása. A német kormány támogatását élvező Car2Car kutatási projektet az RDC szaktudással és életciklusuk végéhez ért modellekkel segíti. Tavaly a projekt szakértői olyan módszereket dolgoztak ki, amelyek lehetővé teszik, hogy az életciklusuk végéhez ért autókban felhasznált acél, alumínium, réz, üveg és műanyag alapanyagokat minden korábbinál nagyobb arányban hasznosíthassák újra a sorozatgyártásban készülő új modellekben.
A BMW Group konzorciumvezetőként is részt vesz a Car2Car kutatási projektben, amelynek égisze alatt az újrahasznosítási iparág tagjaival, nyersanyag-feldolgozó vállalatokkal és tudósokkal is együttműködik. A projekt a különböző újrahasznosítási eljárások gazdasági és környezeti hatásainak kiértékelését tekintve látványos előrelépéseket mutat. A szaktudás megosztása és a közös munka új nézőpontokat eredményezett a maradékanyagok újrahasznosítása terén, egyúttal stabil alapot biztosított az innovatív folyamatok kidolgozásához. A tudósok és az iparági szakértők például az olyan félautomatizált szétszerelő folyamatok kifejlesztésén is közösen dolgoznak, amelyek az újrahasznosítható anyagok költséghatékony szétválasztását teszik lehetővé.
Körforgásos tervezés a zárt anyagciklus érdekében
Mindazon szaktudást, amit az RDC az alkatrészek és alapanyagok újrahasznosíthatósága terén halmoz fel, a BMW Group a terméktervezési folyamatokba is visszavezet. Re:Think, Re:Duce, Re:Use és Re:Cycle alapelvei mentén a vállalatcsoport célja, hogy olyan autókat gyártson, amelyek hasznos életciklus-fázisuk végén – amely Németországban átlagosan 21 év – teljes egészében nyersanyagforrásként szolgálhatnak az újonnan készülő autók számára. A kulcs e téren a monoanyagok alkalmazása a kompozitok helyett, hiszen nagyobb tisztaságukkal könnyebben újrahasznosíthatók.
Üzemei sorozatgyártási folyamatait a BMW Group világszerte továbbfejleszti az RDC által elért kutatási eredményekkel: az új autók gyártása során preferenciát élveznek azok a módszerek, amelyek megkönnyítik az alkatrészek szétszerelését és az anyagok típus szerinti szétválasztását. A ragasztást például az innovatív csatlakoztatási megoldások váltották fel.
Zárt újrahasznosítási ciklus a nagyfeszültségű akkumulátorok esetében is
Az elektromos mobilitás térnyerésével a nagyfeszültségű akkumulátorok újrahasznosítása is egyre inkább központi tényezővé érik. Az RDC az iparág és az akadémia szakértőivel karöltve már évek óta dolgozik a nagyfeszültségű akkumulátorok innovatív újrahasznosítási módszereinek kifejlesztésén.
Az RDC iránymutató az autóipar körforgásossága felé vezető úton. Az újrahasznosítás területén elért úttörő eredményeivel a központ már három évtizede támogatja az új modellek, anyagok és technológiák kifejlesztését. Az elektromos mobilitás korában az RDC feladatköre az értékes erőforrások újrafelhasználása terén felhalmozott szaktudás elmélyítésével és az újrahasznosítási iparág számára történő átadással bővült. Az autóipari újrahasznosítás szakértő központjaként így az RDC folyamatosan szélesíti szerepkörét. Most, amikor a körforgásos gazdaság az autóipar jövőjét tekintve egyre fontosabbá válik, az RDC tapasztalatára és szaktudására minden korábbinál nagyobb szükség van.
Forrás: BMW Magyarország
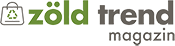
Zöld Közlekedés
Gyors, menő, de veszélyes: így készülj az iskolai e-rolleres közlekedésre az őszi hónapokban
Iskolába e-rollerrel? 5 fontos tipp Bécstől a biztonságos közlekedéshez.
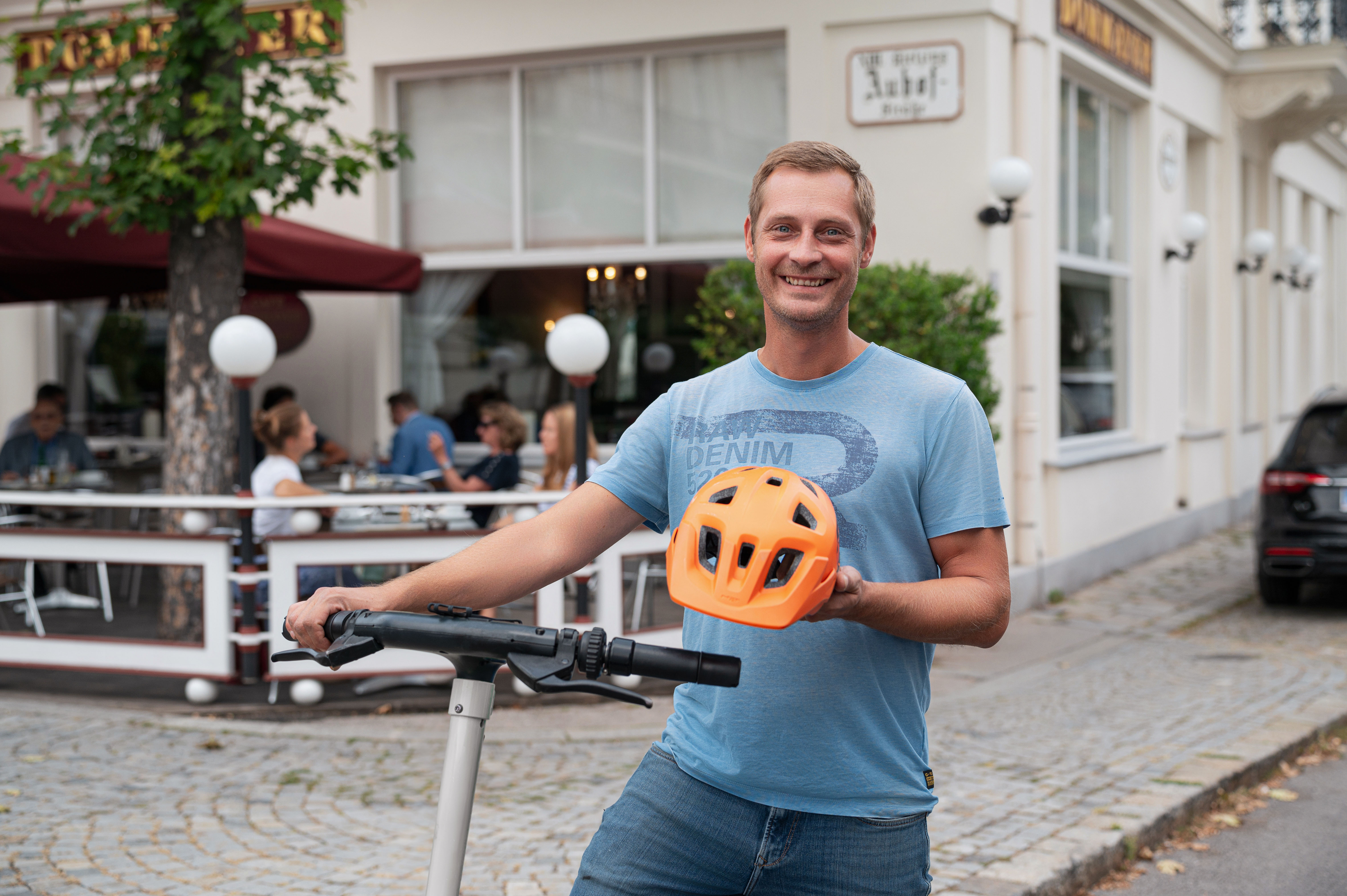
Töltse ki a napelem-kalkulátort, és tudja meg, mennyibe kerülhet Önnek! Ingyenes kalkulálás itt (x)
Az iskolakezdés közeledtével egyre többen választják az elektromos rollert az iskolába járáshoz, mivel gyors és kényelmes közlekedési eszköz – hívja fel a figyelmet az alternativenergia.hu. Bécsi szakértők azonban arra figyelmeztetnek, hogy a rollerrel való közlekedés fokozott odafigyelést igényel, különösen gyermekek esetében. Ahogy egyre több gyerek választja az elektromos rollert az iskolába menet, úgy válik egyre fontosabbá a biztonságos közlekedésre való felkészülés is. A nyár vége ideális időszak arra, hogy a gyerekek (és szüleik) megismerkedjenek a helyes használattal és a lehetséges veszélyekkel. Az őszi hónapok ugyanis nemcsak hűvösebbek, hanem csúszós, esős időjárással, lehullott falevelekkel és gyengébb látási viszonyokkal is járnak, amelyek jelentősen növelhetik a balesetek kockázatát. Karl Schlosser, a Bécsi Gazdasági Kamara Autósiskolákért felelős részlegének vezetője – aki egyben tapasztalt e-roller oktató is- szerint éppen ezért érdemes már most, a nyári időszakban elkezdeni a felkészülést, hogy az iskolakezdésre a gyerekek magabiztosabban és biztonságosabban közlekedjenek.
A szakértők ezért öt alapvető szabály betartását javasolják minden rollerhasználónak:
- Tartsd be a közlekedési szabályokat és légy tekintettel másokra!
- Mindig viselj bukósisakot, hiszen az életet menthet!
- Gondoskodj arról, hogy a roller mindig jó műszaki állapotban legyen, működjön a világítás és legyen rajta csengő!
- Légy jól látható, különösen sötétedés után viselj világos, feltűnő ruházatot!
- Kanyarodáskor mindig jelezd szándékodat kézjelekkel vagy irányjelzővel!
A 2024-es bécsi baleseti statisztikák szerint 27%-kal több e-rolleres balaset történt, mint egy évvel korábban, jellemzően figyelmetlenség és hiányos ismeretek miatt. A bécsi autósiskolák ezért speciális, gyerekeknek és felnőtteknek szóló tanfolyamokat kínálnak, ahol a résztvevők elsajátíthatják a biztonságos e-roller és e-kerékpár használat alapjait. A képzések során a közlekedési szabályok mellett gyakorlati tippek is elhangzanak, például, hogy hogyan kell helyesen fékezni, kanyarodni vagy megközelíteni a kereszteződéseket.
-
Zöldinfó2 nap telt el a létrehozás óta
Medvék és emberek konfliktusa: országos vizsgálat indul a barnamedve-állományról
-
Zöld Energia8 óra telt el a létrehozás óta
Magyarország kincset rejt a föld alatt – most dől el, hogyan használjuk ki
-
Zöldinfó2 nap telt el a létrehozás óta
Hat új helyszínen indul szénhidrogén-kutatás – jön az energiabiztonság új korszaka?
-
Zöldinfó5 óra telt el a létrehozás óta
Téli rezsicsúcs helyett fix havi díj – változás jön a villanyszámlák elszámolásában
-
Zöld Energia6 nap telt el a létrehozás óta
Itt a lehetőség: geotermikus fejlesztésekre indulnak a támogatási programok